

Spotting Drills – short drills used to create shallow or pilot holes.Below are a few special drill bits along with their specific uses. Like with turning operations, different drill bits exist for specific drilling operations.
LATHE TURNING FEEDS AND SPEEDS MANUAL
Other options include: rotation of the head on a manual machine or use of multiple axis’ on a CNC machine. Angular drilling requires special work-holding tooling. Some drilling operations need angular drilling. For even more precision, a center drill operation is often added before drilling. Placing the drill bit perpendicular to the workpiece reduces drifting or leading-off.
LATHE TURNING FEEDS AND SPEEDS FREE
The shape of the drill bit helps chips fall away from the workpiece, keeping the workpiece free of debris. Chips are the bits of waste metal produced when machining a workpiece. A drill press or tapping machine is designed for drilling, but this process can also be performed using a milling machine. They’re placed at different angles for a variety of outcomes.ĭrilling creates a round hole in a workpiece. Single point cutting tools used in turning come in various shapes. CNC allows for consistency and efficiency of high production runs. These instructions then get sent to the lathe for completion. With Computer Numerical Control, or CNC, you program all the movements, speeds, and tooling changes into a computer. The downside to manual turning is it requires continuous supervision. Like most machining operations, turning is either done manually or automatically. A lathe is the machine of choice for all turning operations. Turning involves rotation of the work piece while the cutting tool moves in a linear motion. Applying cutting fluid during both cutting phases cools and lubricates the cutting tool. Finishing cuts are typically done at low feeds and depth. After the roughing phase, a finishing cut is applied to achieve final dimensions, tolerances, and surface finish. Their purpose is to get as close to the finished shape and dimensions as possible. Like artistic sculpting, the workpiece first undergoes one or more roughing cuts. Cutting feed refers to how fast the workpiece moves across its axis toward the cutting tool. It’s measured in surface feet per minute. Cutting speed refers to how fast the cutting tool cuts into the workpiece material. The workpiece material, tooling material, and dimensions will influence these parameters. Cutting Speed, Feed Rate, DepthĬutting speed, feed rate, and depth of cut are all parameters to consider when machining. But, opt for carbide to machine tougher and harder tool steels. You may choose to use high-speed steel (HSS) for general purpose milling. The most common are carbide and high-speed steel. Tooling is available in a variety of materials. Unfortunately, proper upkeep of machinery and tooling is where it can get costly.

It is imperative to properly use and maintain the cutting tools for quality purposes. Use multi-point tools for milling and drilling. Use single point tools for turning, boring, and planing. The two basic types of cutting tools are single point and multi-point tools. The desired form of the material will determine what type of tools you’ll need for the job.
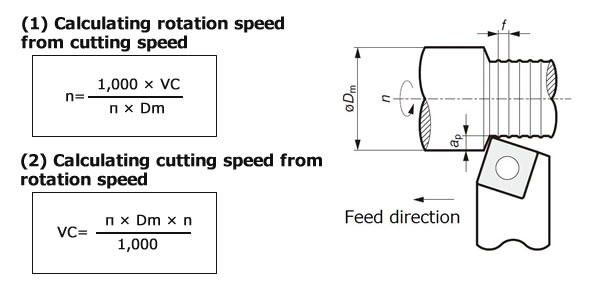

Additive manufacturing requires stacking layers upon layers of material to form a 3D object. In a previous blog, we focused on the future of 3D printing, also known as additive manufacturing.
